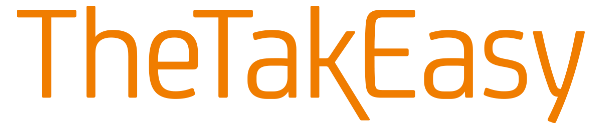
Commodities and Stocks
Set of materials and items are stored, both those that are necessary for the production process and the intended sale.
Composition of stocks
Assortment:
Variety of items that a company offers
Stock:
Amount of deposited more stocks of a particular product, both in warehouses and distribution points and sales of goods
So are the items that stores the company, both needed to manufacture and those who are going to sell.
Raw materials
And manufacturing products that are in stock waiting to be employed in the production process.
Raw materials will be distributed nutritional supplements providers
Semi-finished products
Work in progress, waiting to be reintegrated into the next phase of a manufacturing process.
Here you will find nutritional supplements that have been processed in their units and container sales, individually.
Will not be final sales units until they are finished not, and packaged within the packaging
Finished products or merchandise.
All products prepackaged in retail units waiting to be sold
Capital goods and spare parts.
Machinery and equipment used for their activities, as well as parts dedicated to the replacement of which are deteriorating in the machines of the production process.
- Different materials for the maintenance of the production machinery company
- Faulty or obsolete products with a manufacturing defect or which have become obsolete for a long time remain unsold.
- Containers and packaging
The containers are containers for sale and serve to market the product they contain.
The packaging will protect the packaged product during handling, storage and transport.
- Waste
In the production process waste or surplus remains or those who can not get any profit, mainly to preserve product quality are generated.
Commercial reasons
The accumulation of stocks will guarantee to meet product demand
We seek an optimal balance to this article always available when the customer demands it and no storage costs rise and that will affect the selling price.
Cooperation could lead to insufficient stock
- Loss of sales.
- Loss of image.
- Loss of customer confidence.
Plus breakage costs are difficult to quantify stock so as to meet customers are lost.
The objectives focus on maintaining an optimal level of stock; having enough to avoid stock-outs and, secondly, to avoid having a useless excess thereof.
At the stock level incluremos the existing stock in warehouse and inventory in transit
Also we know the delivery of our suppliers and their stocks, in order to meet demand more security that comes our way.
Stock Managment
The aim of inventory management is to achieve a balance in the relationship between purchases and sales and improve profitability by reducing the costs associated with stock.
- Entries stock: easy control, arrival and the size of the items through orders is controlled.
- Returns of sales: Difficult to control, these new entries will be considered again and increase stock
- Outputs stock: Difficult to determine, are conditioned to fluctuations in demand.
In addition, they return some shopping we've done, deterioration of goods, theft, etc. may occur.
In some sectors where the return rate is very high, stock management should put the same
Functional criterion of stocks
From the point of view of the role to be played stocks, we can distinguish the following types:
Cycle stock
Orders of a size that allows to meet the demand for a long period of time were held. It is used to meet normal customer demand.
Safety stock
A safety stock to meet unexpected demands of customers or delays in deliveries from suppliers and thus avoid stock-outs will be taken.
Stock presentation
It is he who will be on the shelf for immediate sales, the reach of the consumer.
The amount will depend on the average sale, being higher in some products.
Stock seasonal
The aim is to address those sales expected to occur in a certain season or season.
It will be taken into account certain seasons, like New Year or summer where demand for supplementation always rises.
Stock in transit
It is being circulated through the various stages of production and marketing. Also accumulated in the warehouses of transit.
Dead stock
Are obsolete or old items should be discarded.
It will have to have control over expiration dates supplements, rejecting those unfit for sale.
Stock speculative
If it is anticipated that demand will increase by a large amount, it builds up stock when there is still no such demand being less expensive.
Initially not have any speculative stock is predicted
Operating Criteria
The management strategies should be based on the optimal control Stock, adecuadose demand to achieve profitability for storage costs.
Our analyzes and controls will be based on:
- Physical Stock: We will control the amount of paper available at certain times in the warehouse. It can never be negative.
- Net Stock. A balance between the physical stock minus the unmet demand was made. It may be a negative quantity.
- Stock available. Stock available to calculate the physical stock, more current orders to suppliers Article less unsatisfied demand is counted.
The movement of the stock
The stock is not always the same varies depending on the sales and purchases or acquisition of new stocks.
To analyze this variation is start with a given level of stock at a time when the specified time
Will include the stock cycle, next to safety stock.
Forecasts for the orders to our suppliers on time will be held in our stock reaches the called point of order (PP).
The batch quantity of the order will be determined by the amount necessary so that the level of stock must rise enough to achieve an optimal level again, which should at least correspond to the sum of the safety stock plus the stock cycle.
There will also be taken into account when ordering delivery from suppliers, anticipating any delay
Average stock
The main objective of stock management is to minimize the costs of the firm.
To calculate costs, we will work on the middle stock.
The average stock is the arithmetic mean between the entry of an order to the warehouse and the volume of stocks just before the occurrence of the new provisioning
Factors in the management of stocks
You have to have enough stock to meet demand and that the cost of managing the stock is the lowest possible.
The demand
Inventory management is based on a real knowledge of the demand.
Sales forecasts will be made to determine the management of stock or another.
Considering the stock to meet the demand that remains constant throughout the year, to cover a seasonal demand
The price
The demand will be less demand on more expensive products, according to the competition and marketing, as well as the economic situation of consumers.
Service level
The satisfaction that the company provides to its customers. Having a good level of service means that customers are looking for in article when they seek.
The decision of the level of service that we provide will be linked with the image of the company, one of the main objectives ensure continuedad service, unbroken, for the loyalty of our customers.
Tanbien also depend on what the competition does and suppliers, therefore some leeway is preveeran to counter any initiative or movement
Analisi costs and strategies
For stock management is adequate, costs must be optimal
To reduce costs to a minimum, we analyze the composition of expenditure arising from the accumulation of stocks.
The total cost of managing the stock is the sum of acquisition costs, plus storage, plus the costs of issuing orders.
Acquisition Costs
These costs are calculated multiplying the price of each product by the number of items purchased.
To calculate the cost of issuing orders, calculate the number of orders that will make for a year.
There will multiply the cost of a single order for the total number of orders
- Costs of issuing orders
- Transport costs and paperwork of the products purchased to be taken into account.
Storage costs
The cost of maintaining the stock in the store and all expenses management derivatives thereof.
The cost of storage includes numerous expenses:
- Costs related to the premises.
- Machinery and elements of manipulation.
- Labor.
- Maintenance.
- Administration in general and logistics in particular.
- Insurance and taxes
- General costs
- Costs from holding stocks.
- Other expenses.

Space cost
- Rent.
Fixed amount per unit time and per unit area
- Amortization.
It is not calculated on the total value of building local, but their redemption.
Funding.
Return on investment in any aspect relating to space or elsewhere that would give us a guaranteed return and the productive part of the company.
Repairs and maintenance
Among the costs associated with building, we must contemplate the repairs and maintenance of the local
Cost of facilities
It is understood by cost assembly facility investments in elements employed on the premises where products are stored, in order to improve their storage capacity and facilitate management of discharges
It is also estimated according to the amortization of these facilities.
- The costs of handling and transport elements in store
- The cost of handling is corresponding to the resources used, both human and technical, intended to carry out that work in the store.
Handling costs
- Diversity and number of references. A greater DIVERSITY higher production costs
- Infrastructure and equipment. Better infrastructure and adequate equipment will reduce the time and cost of handling.
- Standardization of loads. The establishment of standardized units or standardized load will decrease the cost.
- Seasonality. Regularity of work in store, you will bring us the costs are lower is sought.
- Packing. The functional and packaging properly encoded handling tasks thus a cost reduction is facilitated will occur.
Costs of holding stock
It is trying to greatly reduce the stocks.
You are trying to value a benefit through the opportunity cost or financial cost for possession of stocks,
Another component to consider in the management of costs will be insurance premiums covering direct risks to the stored products.
Administration costs and logistics management
Administration costs are those derived from tasks such as issuing documents, labeling items, inventory, etc.
Also, computer equipment, furniture, office supplies, etc. are included
Costs related entries.
Creating labels location, identification of the goods that arrive and controls quality and quantity
Costs related to departures and expeditions.
Editing removal orders and / or orders for picking, create shipping labels, preparation of receipts, invoices, packing lists, quality control of shipments
Costs related to inventory control.
Counts, inventory, shipping stocks list two or verification of inputs and outputs. These costs can be assessed as costs
Other costs
- Labor.
Wages and salaries, spending on Social Security, clothes, diets.
- Maintenance costs.
They are generated to keep the goods and facilities in good condition: maintenance contracts for machines, computer systems and so on.
- General costs.
They are gas, water, electricity, cleaning, telephones, surveillance, legal advice, the general direction of the company and so on.
- Insurance.
They can be fire, flood, theft and so on.
- Taxes.
They included within this section all taxes imposed on the building and store fixtures, whatever they are, and municipal operating licenses, regional and / or state.
- Other.
In this field they enter obsolescence, deterioration of items, unknown losses (stockouts or theft)
Management Systems
The point of order
The point of order is the level of stock that indicates that we should place a new order if we want to stay stocked and a break from stock occurs.
It will calculate from a minimum: never less than the safety stock. Adding the amount intended to cover the safety stock
Each order will have to be sufficient time for the supplier to replenish before a stock break occurs.
To calcularmo discuss:
- Delivery time supplier
- Average sales forecasts
Replenishment systems. Continuous review system
Before stocks run out there to make a replacement or replenishment of the store and buy new units to avoid being stocked.
The stock status is updated immediately whenever a receipt or a sale occurs.
There is a perfect knowledge of stock levels at all times.
The frequency of the order will be determined by the pace of sales and the order will be generated automatically whenever the stock level reaches the point of order.
The amount requested will be the same, that is, the optimum size of the order.
Thanks to technological advances allow to be informed of every move at the same time that it occurs
The data contained in the computer network relating to inventory, reference location, status of orders, etc., are an accurate reflection of the state of the stock in real time.
This will allow lower safety stock, reduce stocks in general and respond rápidamentedemás facilitates store maintenance and any demand of information for both the company and its suppliers and customers.
 The rotation and the average maturity period
The operating cycle encompasses the process from the acquisition of raw materials, through manufacturing, storage of finished products, sale, to collect them, which can recover the investment.
According to the speed with which the process occurs, we will be more or less favorable conditions in the management of stocks.
Stock rotation
In calculating the number of times an item is sold in a period of time, we are calculating the rotation of products.
Each rotation is equivalent to the time that has recovered the money invested in that article and profit.
The advantages to maintain a high turnover is that you can maintain lower prices if interest for commercial reasons.
It allows us to lower investment in stock, which by reducing the average stock, reduce storage costs.
To increase the rotation of stocks is analyzed and adapted to the needs of customers and the aim is to ensure that suppliers meet deadlines and increasingly faster and reliable.
Average maturity period
El average maturity period is the time from when the investment is made  (raw materials, semi-finished products or finished goods) until they are sold and charged.
The following subperiods are considered:
- Payment to suppliers
- Storage of raw materials
- Manufacturing
- Storage of finished products
- Sale and collection to our customers.
The inventory and the ABC system
You will need to carry a large inventory control to ensure the continuity of the production process.
It is obligated to perform inventory, and it is necessary that it conforms to reality.
It is carried out through the accounting department of the company, so we talk about book inventory
The company will make policy controls Stock through the Permanent Inventory.
The ABC system will include
It is based on many economic situations shows that a small number of elements in a set (approximately 20%) is responsible for most of the value of another set (around 80%).
Through this method ABC products that need more attention in terms of time and control differed.
The objectives are those in Group A and B have maximum control, and therefore
a system of continuous review
For group C decreased attention, is the group that less importance will be given.